Processing process analysis
The copper sleeve part of the nozzle hole is shown in Figure 1. The nozzle hole processing and the nozzle hole cutting groove are all completed by the imported machining center and special plane, and the processing size and positional accuracy fully meet the product design requirements.
figure 1
The artificial deflashing function is to remove the flash edges of each surface to ensure the appearance quality. The automatic cleaning function of the cylinder head ensures that all parts of the cylinder head are clean and meet the requirements of subsequent press fitting and assembly. The artificial blowing chip is a chip that can not be cleaned by the casting cavity, and is manually blown off by an air gun.
The sealing ring is manually placed into the nozzle hole sealing groove, and the sealing device automatically presses the copper sleeve into the nozzle hole and expands the small head by the expansion rod. The large copper sleeve is sealed by the sealing ring, and the small sleeve of the copper sleeve is expanded and sealed.
Sealing and leak testing is to check for leaks in various parts of the waterway by airtight test. If the copper sleeve is not tightly sealed, air leakage will occur.
Troubleshooting and improvement
Leakage of the copper head seal or the small head seal may cause malfunction. In order to determine the leaking part, a manual plugging device was adopted (the device was internally filled with liquid), and 20 sets of copper sleeve leaking cylinder caps were randomly selected for liquid filling test. The conclusion was that all the copper holes of the nozzle hole leaked.
For the water leakage in the large part of the copper hole of the nozzle hole, the fish thorn diagram is used for the cause analysis (see Figure 2).
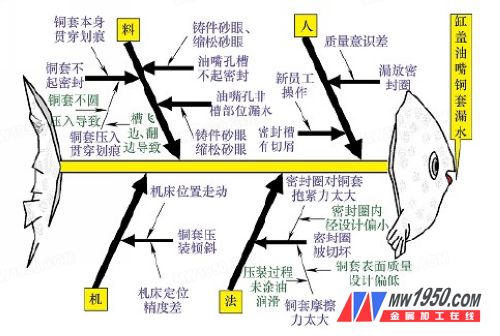
Fig.2 Analysis of the causes of water leakage in the cylinder head of the cylinder head
Through continuous statistics of 200 leaking copper bushings, it was found that two leaking seals and three seals had chips. Proportionally this is not the main reason, but it is still one of the causes of water leakage and needs to be controlled.
Leaking the sealing ring is due to the lack of responsibility of the operator. The inspector did not monitor the rework process and only monitored the rework results, resulting in the failure to handle the leaking seal.
The sealing groove has chipping, because the cutting process in the front of the sealing ring and the manual cutting of the inner cavity of the cylinder head chip, because there is no standard blowing chip order and attention point, the individual chips are blown into the sealing groove.
In response to the above factors, all the personnel who put the sealing ring will be trained, and the cutting staff will finally blow the nozzle hole sealing groove, and make a copper sleeve leaking rework process record table. The re-work process of the production line copper sleeve leaking copper bushing must be carried out under inspection supervision. It was found that the leakage sealing ring and the sealing groove had iron filings to be evaluated by the responsible person.
2. Machine factors
The action process of the equipment is as follows: the copper sleeve mechanism uses the copper sleeve to fall freely into the nozzle hole by the self-weight, and the pressure rod pushes the copper sleeve into position. Through equipment inspection, it is found that the center of the copper sleeve and the copper sleeve mechanism of the machine tool is different from the center of the cylinder head nozzle hole, and the deviation is 0.3 mm. This deviation may cause the copper sleeve and the nozzle hole wall and the sealing ring to collide with each other to cause water leakage.
In order to avoid water leakage caused by different press fittings of the equipment, special inspection tools are prepared, and the equipment is adjusted to ensure that the center of the pressure bar and the center of the nozzle hole are on the same axis (see Figure 3). It has been verified that the leakage ratio of the copper sleeve is not significantly reduced, and the difference in equipment is not the main cause of water leakage.
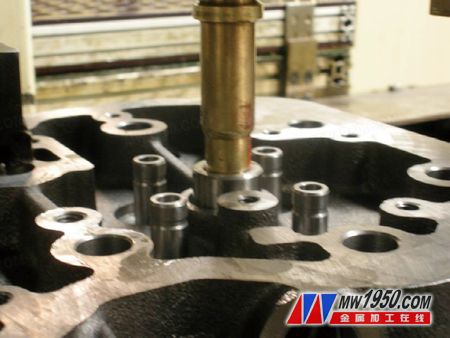
image 3
Re-arguing whether the seal ring is cut when pressed into the seal, check the seal ring, using the cut-resistant fluoroelastomer material; check the surface roughness of the copper sleeve.
After inspection, the surface quality of the copper sleeve completely conforms to the requirements of the drawings, and there is basically no sharp corner in the transition plane; the copper sleeve has been lubricated according to the requirements before the press fitting, and the above methods are controlled, which is not the main reason for water leakage.
4. Factors of the material
In order to prove that the copper sleeve is not sealed or the cylinder head nozzle groove is not sealed, the company conducted a detailed experimental study. Redesigned and modified a set of manual plugging device, changed the filling test mode to the inflation test mode, and remade the inflatable joint device (see Figures 4 and 5).
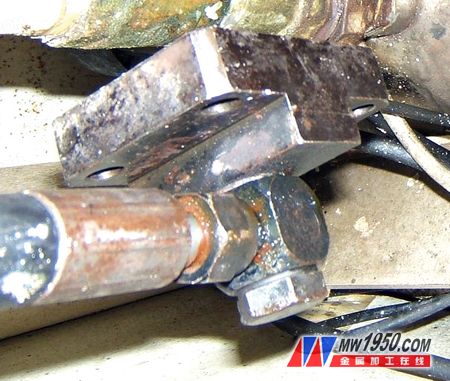
Figure 4
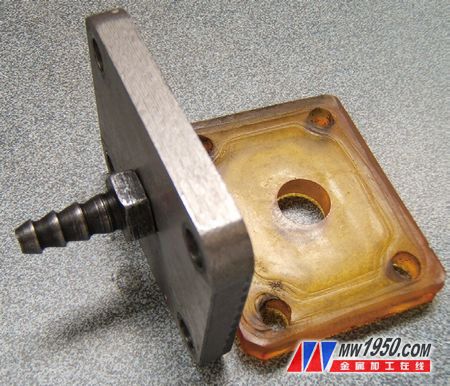
Figure 5
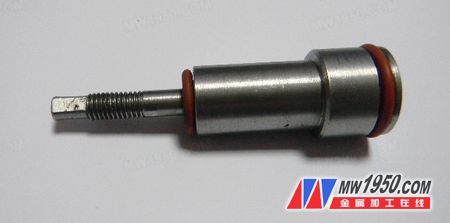
Image 6
1) There is casting shrinkage or blistening in the nozzle hole of the cylinder head, which leads to leakage of water in the non-sealed groove or seal seal of the sealing groove.
2) There is a scratch on the copper cover of the cylinder head, which causes the seal of the seal to not leak.
The above two points are the main reasons for the leakage of the copper cover of the cylinder head, and the deeper reasons for finding and implementing the improvement are respectively carried out.
The oil hole is provided with a trachoma shrinkage leaking cylinder cover for analysis by the blank casting manufacturer, and the defective nozzle hole portion is cut, and the leaking point is confirmed by pumping water (see FIG. 7) and the infiltration method, and the leak point is verified. Therefore, our company and the blank casting manufacturer have made clear that there are large defects observed by the naked eye in the nozzle hole of the cylinder head, and the blank is directly judged as waste; the leakage of the copper cover of the cylinder head reveals that there are small defects in the nozzle hole, and during the improvement of the blank casting, the copper sleeve is pressurized. The blank is still directly judged to be a scrap.
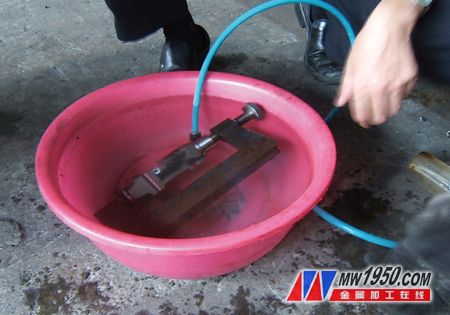
Figure 7
1) The surface of the copper sleeve itself has scratches, and the copper sleeve material is soft, which is easy to produce scratches during the manufacturing process or packaging transportation.
2) The copper sleeve is not round, the outer diameter of the copper sleeve is φ26g7, and the inner circle of the cylinder head nozzle hole is φ26H7. If the copper sleeve is not round, the copper sleeve will be scraped into the through hole by the nozzle hole wall when entering the nozzle hole.
3) There is a machining flash on the surface of the cylinder head nozzle groove and the through hole, which causes the copper sleeve to be scraped through the scratch when entering the cylinder head nozzle hole.
For the above reasons, take the following measures:
(1) The scratch problem of the copper sleeve itself is specified. When the operator takes the copper sleeve, the appearance of the copper sleeve is visually inspected. It is found that the sealing surface area has a scratch through the line, and the problem is fed back to the copper sleeve manufacturer for improvement.
(2) The problem of non-circular copper sleeve is judged by φ26mm sample circle. The copper sleeve does not pass the sample circle, and the copper sleeve manufacturer is required to pass the copper sleeve through the φ26mm sample circle as one of the acceptance criteria (see Figure 8). For this reason, the copper sleeve manufacturer first tested the qualified copper sleeves with 100% of the micrometers. The test proved that the qualified copper sleeves were accepted and the scratches in the press-fit process were significantly reduced. The copper sleeve manufacturers made 100% inspection and control copper. Set of quality of supply.
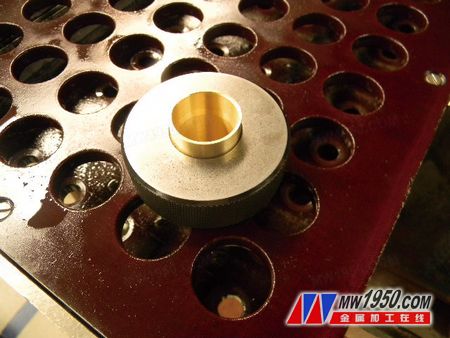
Figure 8
For many water leakage cases, no foundry sand shrinkage was found after the copper sleeve was pulled out. No cylinder heads were found for leaking seals, sealing groove chips, etc., and then the electric grind head was used to polish the through holes of the nozzle holes to remove sharp corners. Completely eliminate the flashing and flanging. After verification, the copper sleeve will not be leaked again.
Conclusion
Through the improvement of the cylinder head casting of the purchased blank manufacturer, the leakage ratio of the nozzle hole and the looseness of the nozzle hole is greatly reduced. According to statistics, the scrapped parts of the nozzle hole casting defects were reduced from 54 pieces before the improvement to 3 pieces after the improvement.
The appearance and roundness of the copper sleeve of the purchased copper sleeve manufacturer are improved. The quality control of the sealing ring and the blowing chip is strengthened through internal production management. The technical management strengthens the quality control of the sealing groove and the through-hole flanging, and the equipment management strengthens the copper pressure. Set of concentricity prevention and control. After the above measures were put in place, the effect was obtained: the leakage ratio of the cylinder head copper sleeve was reduced from 4.7% before the improvement to 0.87% after the improvement.
The troubleshooting and improvement involves a wide range. The company started with the whole process flow, and used the fishbone diagram to analyze the possible factors of human, machine, material, law and ring, and verified by verification methods, and finally solved the problem. It has improved the material support capability, equipment support capability, personnel operation control support capability, and process means support capability, and provided troubleshooting and improvement research directions for leaks similar to seal structures.
Safety Valve,Right Angle Safety Valve,Stainless Steel Safety Valve,Pressure Reducing Safety Valve
Jiangsu Hida Marine Valve Co., Ltd , https://www.haidavalve.com