1 INTRODUCTION <br> before ethylene is one of important petrochemical basic raw material production, widely used in synthetic fibers, synthetic rubbers, plastics production. The production of ethylene represents the level of development of a country's petrochemical industry. China's ethylene production started late, but it has developed rapidly, from tens of thousands of tons per year in the 1950s to tens of millions of tons today. Nowadays, a number of large-scale ethylene production enterprises have been built in China, and a large number of small and medium-sized enterprises producing ethylene are scattered throughout the country. The development of ethylene not only promotes the development of the petrochemical industry, but also plays an increasingly important role in the entire national economy.
The raw materials for the production of ethylene are natural gas, naphtha and refinery products (such as atmospheric diesel, vacuum diesel, etc.). Ethylene production has greater fire and explosion hazard than refining, higher production pressure (maximum operating pressure of 11.28 MPa), higher temperature (maximum temperature up to 1010 ° C), more complex equipment, more continuous, and still There is cryogenic operation (minimum temperature reaches -170 °C), and the materials in the production process are mostly gaseous. Therefore, it is extremely important to do a good job in fire prevention and explosion prevention. The author analyzes the fire hazard of the ethylene production process and proposes fire prevention measures for discussion.
  2 ethylene production process <br> ethylene production (simultaneous production of propylene) as process flow shown in FIG.
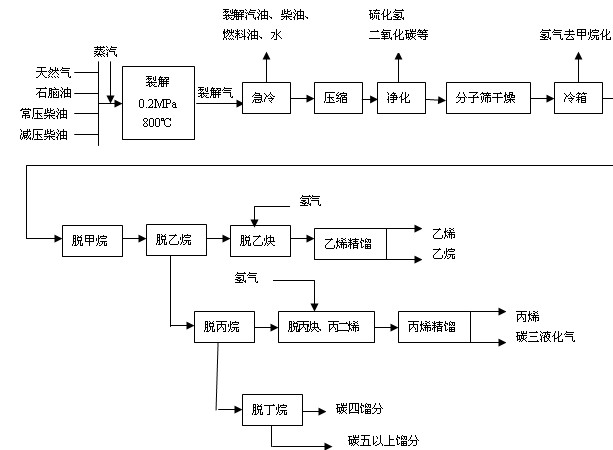
3 Fire hazard of ethylene production <br> Fire hazard of ethylene production In addition to the fire hazard of ordinary refinery, some of the fire hazards of the process have the following characteristics:
3.1 Cracking <br> Ethylene production is carried out under high temperature and pressure. If the temperature at the time of cracking is greater than 800 ° C, the cracked products are mostly in a gaseous state. The operating temperature of the cracking is much higher than the spontaneous ignition point of the material. Once it leaks, it will spontaneously ignite spontaneously; if it is mixed with air to reach the explosive concentration, it will explode in the event of an open flame, and the production process will have an open flame in the heating furnace.
  3.2 Compression <br> Compression is the compression of raw materials through a compressor to 3.0 ~ 4.0MPa. If the equipment is not in good quality, the equipment is poorly maintained or in disrepair, and the operation is caused by negative pressure or overpressure, or due to poor cooling of the compressor, poor lubrication, material leakage due to corrosion or cracks in the pipeline or equipment, equipment will occur. Explosion and rushing, causing a fire accident.
3.3 Deep cooling <br> Deep cryogenic separation is carried out at an ultra-low temperature of -30 to -165 °C. If the raw material gas is not dry and the equipment system remains hydrated, “freezing plugging†will occur. In addition, when the equipment is parked and discharged, the equipment is cold and brittle due to the strict observance of the process operation rules, resulting in a large amount of leakage of combustible materials in the welds of the equipment and joints, which may cause fire and explosion accidents.
  3.4 Hydrogenation <br> The hydrogenation process is the addition of hydrogen to acetylene, carbon three, and gasoline. Hydrogen is a flammable, explosive, and highly permeable gas, so the hydrogenation process is very strict. If the hydrogen and alkyne ratios of the feed to the hydrogenation reactor are not properly controlled, the hydrogenation reactor will be "flying warm" (sudden temperature rise). If the reaction temperature of the reactor is too high, it will cause coking of the catalyst, causing the reactor to "fly". If the "flying temperature" is severe and the temperature of the reactor rises sharply, hot creep will occur on the wall, causing a fire or even an explosion.
In addition, the ethylene plant often stores a large amount of liquefied petroleum gas, and the liquefied petroleum gas tank area also has a great fire and explosion hazard.
4 fire prevention measures <br> according to the fire risk of the ethylene production process, we believe that the production of ethylene fire prevention measures following should be noted.
4.1 Strict control of operating temperature <br> The cracking separation process is carried out in a production unit with high degree of automation and continuity. To strictly control the temperature, automatic temperature measurement, automatic temperature adjustment and interlocking system should be installed. The important part should be equipped with a lower temperature and upper temperature alarm device. When the temperature is exceeded, it can automatically cool down, relieve pressure, cut off the feed valve, and vent the air. In particular, when the device is opened or stopped, the process operation rules must be strictly implemented to determine the process parameters such as oven heating curve, constant temperature and temperature drop. In the hydrogenation process, it is necessary to closely monitor whether the control of hydrogen and alkyne ratio meets the specifications of the process and prevent the hydrogenation reactor from "flying temperature". If the interlocking device fails during the "flying temperature", the process measures of cutting off the hydrogen and materials, stopping the heating, closing the inlet and outlet valves and emergency venting should be taken immediately.
  4.2 Strict control of pressure <br> In the process of ethylene production, if the pressure is too high, it will cause equipment, pipes to burst or react violently and explode. If the equipment and piping produced by positive pressure form a negative pressure, the air is drawn into the equipment and mixed with flammable and explosive materials, posing a fire or explosion hazard. Negative pressure production equipment and pipelines, if there is positive pressure, flammable and explosive materials leak out, fires and accidents will occur, so:
4.2.1 The risky compression and cryogenic separation process shall be provided with automatic pressure regulation, automatic alarm (including low pressure alarm, high pressure alarm, dangerous pressure alarm), automatic resection and other control pressure control systems. The pyrolysis gas at high temperature is insufficient due to water stoppage and water pressure, or the gas pressure is greater than the water pressure and cannot be cooled down. It will cause equipment to cause fire. Therefore, it should be equipped with two power sources and water sources. If it is greater than the air pressure, it should be emptied urgently when the water is stopped or the air pressure is greater than the water pressure.
4.2.2 In order to accurately measure the pressure of each part of the process system, the selected pressure gauge should have sufficient accuracy and regular calibration. The maximum range should be compatible with the working pressure on the vessel.
  4.3 Strict control of material flow rate, flow rate and liquid level <br> Hydrocarbon gas and liquid in ethylene production will generate static electricity. To limit the generation of static electricity, the flow rate of materials in the pipeline should be strictly controlled. It is necessary to strictly control the proportion, speed and quantity of the feed. If the feed is excessive and the volume expands after the temperature rises, the equipment or container may burst. The liquid level of towers, tanks and containers must be closely monitored. The liquid level is too low to pump equipment. If the liquid level is too high, it is easy to run and take materials. In order to ensure safe production, low-level or high-level automatic alarm and automatic cutting and feeding control system should be set on the tower, tank and container. In particular, the liquid level of the suction tank of each section of the compressor should be strictly controlled to prevent the instrument interlocking failure when the high liquid level is high. The gas will run into the compressor with the liquid, causing vibration, causing damage to the tank, and a large amount of material spilling and causing a major accident. .
  4.4 Installation of safety devices <br> Pressure vessels and equipment should be equipped with explosion-proof pressure relief and other safety devices such as safety valves, pressure gauges and rupture discs. The safety valve on the flammable, explosive, and toxic material container should be led to the flare system for burning when it is drained. Pressure gauges must be selected. It is strictly forbidden to use copper pressure gauges and valves on ammonia and acetylene pipes or equipment. Pressure gauges must be installed vertically on pipes and equipment. A flame arrester or water seal should be installed on the pipeline connected to the high temperature equipment or the open flame heating furnace to prevent the fire from expanding when the fire is on fire. A check valve is installed on the pipe produced under different pressures or between the equipment to prevent the gas or liquid from flowing backwards, and to prevent the high-pressure system gas or liquid from entering the low-pressure system and causing an explosion. Install a breathing valve on the tank to prevent the tank from being twitched and overpressured. All explosion-proof pressure relief and safety devices or accessories must be visually inspected monthly for periodic verification to ensure accuracy and safety.
  4.5 Frequently repaired equipment <br> Ethylene production is high temperature, high pressure and extremely corrosive. Various equipments, containers and pipelines are prone to leakage and fire accidents due to long-term scouring, corrosion, wall and tank walls. Therefore, it is necessary to carry out major overhaul of the device in a timely manner. It is necessary to organize engineering technicians to analyze and consult on key equipment, containers and key parts, and apply modern testing methods and methods such as physical flaw detection and filming to meticulously overhaul and eliminate hidden dangers.
  4.6 Fire-fighting facilities <br> It is necessary to equip the fire-fighting equipment according to the characteristics of the device. Such as cooling water systems, foam fire extinguishing systems, automatic sprinkler systems, steam fire extinguishing systems. When a large amount of flammable and explosive gas leaks in the device, in order to avoid explosion in contact with the open flame heating furnace, a combustible gas automatic detection and alarm device may be installed between the open flame zone and the flammable gas leakage zone to fix the steam fire extinguishing system. Because high-temperature equipment can't save water and foam, setting up a steam fire-extinguishing system has a special effect on the initial fire of high-temperature equipment that saves thermal cracking.
  5 Conclusion <br> fire protection requirements ethylene production enterprises, "fire protection design of petrochemical enterprises" (GB50160) and other fire codes have made a more detailed and comprehensive provisions, only the author of several special ethylene production process of fire The hazard was analyzed and some shallow understandings were made for these fire hazards for reference by fire supervisors and relevant personnel in ethylene production enterprises.
(Responsible editor Guo Fengqin)
The raw materials for the production of ethylene are natural gas, naphtha and refinery products (such as atmospheric diesel, vacuum diesel, etc.). Ethylene production has greater fire and explosion hazard than refining, higher production pressure (maximum operating pressure of 11.28 MPa), higher temperature (maximum temperature up to 1010 ° C), more complex equipment, more continuous, and still There is cryogenic operation (minimum temperature reaches -170 °C), and the materials in the production process are mostly gaseous. Therefore, it is extremely important to do a good job in fire prevention and explosion prevention. The author analyzes the fire hazard of the ethylene production process and proposes fire prevention measures for discussion.
  2 ethylene production process <br> ethylene production (simultaneous production of propylene) as process flow shown in FIG.
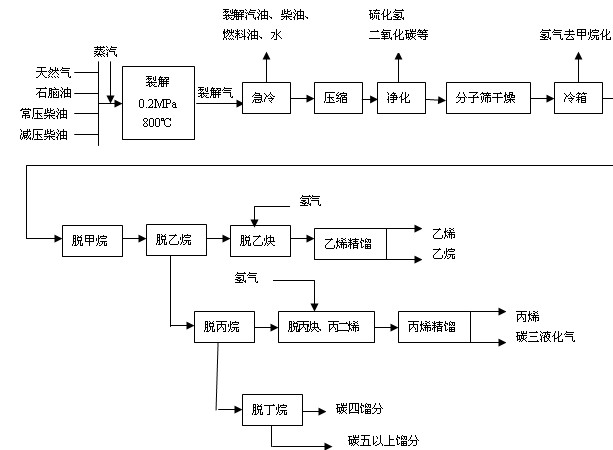
3 Fire hazard of ethylene production <br> Fire hazard of ethylene production In addition to the fire hazard of ordinary refinery, some of the fire hazards of the process have the following characteristics:
3.1 Cracking <br> Ethylene production is carried out under high temperature and pressure. If the temperature at the time of cracking is greater than 800 ° C, the cracked products are mostly in a gaseous state. The operating temperature of the cracking is much higher than the spontaneous ignition point of the material. Once it leaks, it will spontaneously ignite spontaneously; if it is mixed with air to reach the explosive concentration, it will explode in the event of an open flame, and the production process will have an open flame in the heating furnace.
  3.2 Compression <br> Compression is the compression of raw materials through a compressor to 3.0 ~ 4.0MPa. If the equipment is not in good quality, the equipment is poorly maintained or in disrepair, and the operation is caused by negative pressure or overpressure, or due to poor cooling of the compressor, poor lubrication, material leakage due to corrosion or cracks in the pipeline or equipment, equipment will occur. Explosion and rushing, causing a fire accident.
3.3 Deep cooling <br> Deep cryogenic separation is carried out at an ultra-low temperature of -30 to -165 °C. If the raw material gas is not dry and the equipment system remains hydrated, “freezing plugging†will occur. In addition, when the equipment is parked and discharged, the equipment is cold and brittle due to the strict observance of the process operation rules, resulting in a large amount of leakage of combustible materials in the welds of the equipment and joints, which may cause fire and explosion accidents.
  3.4 Hydrogenation <br> The hydrogenation process is the addition of hydrogen to acetylene, carbon three, and gasoline. Hydrogen is a flammable, explosive, and highly permeable gas, so the hydrogenation process is very strict. If the hydrogen and alkyne ratios of the feed to the hydrogenation reactor are not properly controlled, the hydrogenation reactor will be "flying warm" (sudden temperature rise). If the reaction temperature of the reactor is too high, it will cause coking of the catalyst, causing the reactor to "fly". If the "flying temperature" is severe and the temperature of the reactor rises sharply, hot creep will occur on the wall, causing a fire or even an explosion.
In addition, the ethylene plant often stores a large amount of liquefied petroleum gas, and the liquefied petroleum gas tank area also has a great fire and explosion hazard.
4 fire prevention measures <br> according to the fire risk of the ethylene production process, we believe that the production of ethylene fire prevention measures following should be noted.
4.1 Strict control of operating temperature <br> The cracking separation process is carried out in a production unit with high degree of automation and continuity. To strictly control the temperature, automatic temperature measurement, automatic temperature adjustment and interlocking system should be installed. The important part should be equipped with a lower temperature and upper temperature alarm device. When the temperature is exceeded, it can automatically cool down, relieve pressure, cut off the feed valve, and vent the air. In particular, when the device is opened or stopped, the process operation rules must be strictly implemented to determine the process parameters such as oven heating curve, constant temperature and temperature drop. In the hydrogenation process, it is necessary to closely monitor whether the control of hydrogen and alkyne ratio meets the specifications of the process and prevent the hydrogenation reactor from "flying temperature". If the interlocking device fails during the "flying temperature", the process measures of cutting off the hydrogen and materials, stopping the heating, closing the inlet and outlet valves and emergency venting should be taken immediately.
  4.2 Strict control of pressure <br> In the process of ethylene production, if the pressure is too high, it will cause equipment, pipes to burst or react violently and explode. If the equipment and piping produced by positive pressure form a negative pressure, the air is drawn into the equipment and mixed with flammable and explosive materials, posing a fire or explosion hazard. Negative pressure production equipment and pipelines, if there is positive pressure, flammable and explosive materials leak out, fires and accidents will occur, so:
4.2.1 The risky compression and cryogenic separation process shall be provided with automatic pressure regulation, automatic alarm (including low pressure alarm, high pressure alarm, dangerous pressure alarm), automatic resection and other control pressure control systems. The pyrolysis gas at high temperature is insufficient due to water stoppage and water pressure, or the gas pressure is greater than the water pressure and cannot be cooled down. It will cause equipment to cause fire. Therefore, it should be equipped with two power sources and water sources. If it is greater than the air pressure, it should be emptied urgently when the water is stopped or the air pressure is greater than the water pressure.
4.2.2 In order to accurately measure the pressure of each part of the process system, the selected pressure gauge should have sufficient accuracy and regular calibration. The maximum range should be compatible with the working pressure on the vessel.
  4.3 Strict control of material flow rate, flow rate and liquid level <br> Hydrocarbon gas and liquid in ethylene production will generate static electricity. To limit the generation of static electricity, the flow rate of materials in the pipeline should be strictly controlled. It is necessary to strictly control the proportion, speed and quantity of the feed. If the feed is excessive and the volume expands after the temperature rises, the equipment or container may burst. The liquid level of towers, tanks and containers must be closely monitored. The liquid level is too low to pump equipment. If the liquid level is too high, it is easy to run and take materials. In order to ensure safe production, low-level or high-level automatic alarm and automatic cutting and feeding control system should be set on the tower, tank and container. In particular, the liquid level of the suction tank of each section of the compressor should be strictly controlled to prevent the instrument interlocking failure when the high liquid level is high. The gas will run into the compressor with the liquid, causing vibration, causing damage to the tank, and a large amount of material spilling and causing a major accident. .
  4.4 Installation of safety devices <br> Pressure vessels and equipment should be equipped with explosion-proof pressure relief and other safety devices such as safety valves, pressure gauges and rupture discs. The safety valve on the flammable, explosive, and toxic material container should be led to the flare system for burning when it is drained. Pressure gauges must be selected. It is strictly forbidden to use copper pressure gauges and valves on ammonia and acetylene pipes or equipment. Pressure gauges must be installed vertically on pipes and equipment. A flame arrester or water seal should be installed on the pipeline connected to the high temperature equipment or the open flame heating furnace to prevent the fire from expanding when the fire is on fire. A check valve is installed on the pipe produced under different pressures or between the equipment to prevent the gas or liquid from flowing backwards, and to prevent the high-pressure system gas or liquid from entering the low-pressure system and causing an explosion. Install a breathing valve on the tank to prevent the tank from being twitched and overpressured. All explosion-proof pressure relief and safety devices or accessories must be visually inspected monthly for periodic verification to ensure accuracy and safety.
  4.5 Frequently repaired equipment <br> Ethylene production is high temperature, high pressure and extremely corrosive. Various equipments, containers and pipelines are prone to leakage and fire accidents due to long-term scouring, corrosion, wall and tank walls. Therefore, it is necessary to carry out major overhaul of the device in a timely manner. It is necessary to organize engineering technicians to analyze and consult on key equipment, containers and key parts, and apply modern testing methods and methods such as physical flaw detection and filming to meticulously overhaul and eliminate hidden dangers.
  4.6 Fire-fighting facilities <br> It is necessary to equip the fire-fighting equipment according to the characteristics of the device. Such as cooling water systems, foam fire extinguishing systems, automatic sprinkler systems, steam fire extinguishing systems. When a large amount of flammable and explosive gas leaks in the device, in order to avoid explosion in contact with the open flame heating furnace, a combustible gas automatic detection and alarm device may be installed between the open flame zone and the flammable gas leakage zone to fix the steam fire extinguishing system. Because high-temperature equipment can't save water and foam, setting up a steam fire-extinguishing system has a special effect on the initial fire of high-temperature equipment that saves thermal cracking.
  5 Conclusion <br> fire protection requirements ethylene production enterprises, "fire protection design of petrochemical enterprises" (GB50160) and other fire codes have made a more detailed and comprehensive provisions, only the author of several special ethylene production process of fire The hazard was analyzed and some shallow understandings were made for these fire hazards for reference by fire supervisors and relevant personnel in ethylene production enterprises.
(Responsible editor Guo Fengqin)
Kitchen Sink Faucets,Touch Kitchen Faucet,Retractable Kitchen Faucet,Black Steel Hose Faucet
Yuyao Zelin Sanitary Ware Co., Ltd , https://www.kitchen-sinkfaucet.com