Tool wear is one of the most fundamental problems in machining. Understanding the condition and cause of tool wear can help tool manufacturers and users extend the life of CNC tools. Today's CNC tools use coating technology (including the use of new alloying elements), which further extends the life of the tool while significantly increasing productivity.
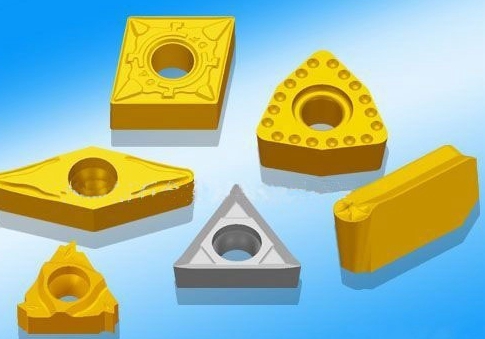
First, the tool wear mechanism introduction:
In metal cutting, the heat and friction generated is a manifestation of energy. The high surface load and the heat and friction generated by the high-speed slip of the chips along the rake face of the tool place the tool in a challenging machining environment.
The amount of cutting force tends to fluctuate up and down, depending on different processing conditions (such as the presence of hard components in the workpiece material, or intermittent cutting). Therefore, in order to maintain its strength at high cutting temperatures, the tool is required to have some basic characteristics including excellent toughness, wear resistance and high hardness.
Although the cutting temperature at the tool/workpiece interface is a key factor in determining the wear rate of almost all tool materials, it is difficult to determine the parameter values ​​required to calculate the cutting temperature. However, the measurement results of the cutting test can lay the foundation for some empirical methods.
It can usually be assumed that the energy generated in the cutting is converted into heat, and usually 80% of this heat is carried away by the chips (this ratio varies depending on several factors - especially the cutting speed). About 20% of the rest of the heat is transferred to the tool. Even when cutting steel parts with less high hardness, the tool temperature may exceed 550 ° C, which is the highest temperature that high speed steel can withstand without reducing the hardness. When cutting hardened steel with polycrystalline cubic boron nitride (PCBN) tools, the temperature of the tool and chips will typically exceed 1000 °C.
Second, tool wear and tool life
Tool wear usually includes the following types: 1 flank wear; 2 scribe wear; 3 months gingival wear; 4 cutting edge blunt; 5 cutting edge chipping; 6 cutting edge crack; 7 catastrophic failure.
There is no universally accepted definition of tool life, usually depending on the different workpiece and tool materials, as well as the different cutting processes. One way to quantify the end of tool life is to set an acceptable maximum flank wear limit (in VB or VBmax). Tool life can be expressed by the Taylor formula of the expected tool life, ie VcTn=C. A more common form of this formula is VcTn×Dxfy=C where Vc is the cutting speed; T is the tool life; D is the depth of cut; For feed rate; x and y are determined experimentally; n and C are constants determined from experimental or published technical data, which represent characteristics of tool material, workpiece and feed rate.
The evolving best tool base, coating and cutting edge preparation techniques are critical to limiting tool wear and resisting cutting temperatures. These elements, combined with the chipbreaker and corner radius on the indexable insert, determine the suitability of each tool for different workpieces and machining operations. The best combination of all these elements extends tool life and makes machining more economical and reliable.
Third, change the tool base
By varying the grain size of tungsten carbide in the range of 1-5 μm, tool manufacturers can change the matrix properties of cemented carbide tools. The particle size of the matrix material plays an important role in cutting performance and tool life. The smaller the particle size, the better the wear resistance of the tool. Conversely, the larger the particle size, the better the toughness of the tool. Fine particle matrix is ​​mainly used for the processing of blades of aviation grade materials such as titanium alloys, Inconel alloys and other superalloys.
In addition, a better toughness can be obtained by increasing the cobalt content of the cemented carbide tool material by 6% to 12%. Therefore, the specific machining requirements can be met by adjusting the cobalt content, whether it is toughness or wear resistance.
The performance of the tool substrate can also be enhanced by forming a cobalt-rich layer near the outer surface, or by selectively adding other alloying elements (such as titanium, tantalum, vanadium, niobium, etc.) to the cemented carbide material. The cobalt-rich layer significantly increases the strength of the cutting edge, which improves the performance of roughing and interrupted cutting tools.
In addition, when selecting the tool base that matches the workpiece material and processing method, it also considers the other five matrix properties - fracture toughness, transverse fracture strength, compressive strength, hardness and thermal shock resistance. For example, if a cemented carbide tool has a chipping along the cutting edge, a base material with a higher fracture toughness should be used. In the case of direct failure or breakage of the cutting edge of the tool, the possible solution is to use a base material with a higher transverse breaking strength or a higher compressive strength. For machining applications with high cutting temperatures (eg dry cutting), tool materials with higher hardness should generally be preferred. In the case where it is possible to observe the hot crack of the tool (the most common in milling), it is recommended to use a tool material with better thermal shock resistance.
Optimization of the tool base material can improve the cutting performance of the tool. For example, the base material of the SumoTec insert grade used by Iscar for machining steel has better resistance to plastic deformation, thereby reducing the possibility of microcracking of hard and brittle blade coatings. Through the secondary processing of the SumoTec insert, the surface roughness and microcracks of the coating are reduced, thereby reducing the cutting heat of the blade surface and the resulting plastic deformation and microcracking. In addition, a new type of substrate for processing cast iron blades has better heat resistance and can be processed with higher cutting speeds.
Fourth, choose the right coating
The coating also helps to improve the cutting performance of the tool. Current coating technologies include:
1 Titanium Nitride (TiN) Coating: This is a general-purpose PVD and CVD coating that increases the hardness and oxidation temperature of the tool.
2 Titanium carbonitride (TiCN) coating: By adding carbon to TiN, the hardness and surface finish of the coating are improved.
3 Titanium aluminum nitride (TiAlN) and aluminum titanium aluminum (AlTiN) coating: The composite application of alumina (Al2O3) layer with these coatings can improve the tool life of high temperature cutting. Alumina coatings are especially suitable for dry and near dry cutting. The AlTiN coating has a higher aluminum content and a higher surface hardness than a TiAlN coating with a higher titanium content. AlTiN coatings are commonly used for high speed machining.
4 Chromium nitride (CrN) coating: This coating has good anti-adhesive properties and is the preferred solution against built-up edge.
5 Diamond coating: Diamond coating can significantly improve the cutting performance of non-ferrous materials cutting tools, and is very suitable for processing graphite, metal matrix composites, high silicon aluminum alloy and other high abrasive materials. However, diamond coatings are not suitable for processing steel because its chemical reaction with steel can damage the adhesion of the coating to the substrate.
In recent years, the market share of PVD coated tools has increased, and its price is comparable to that of CVD coated tools. The thickness of the CVD coating is typically 5-15 μm, while the thickness of the PVD coating is about 2-6 μm. The CVD coating produces undesired tensile stress when applied to the tool substrate; while the PVD coating helps to create a beneficial compressive stress on the substrate. Thicker CVD coatings typically significantly reduce the strength of the cutting edge of the tool. Therefore, CVD coatings cannot be used for tools that require very sharp cutting edges.
The use of new alloying elements in the coating process improves the adhesion and coating properties of the coating. For example, Iskar's 3PSumoTec treatment technology improves the toughness, smoothness and chipping resistance of both PVD and CVD coatings. SumoTec coating technology also reduces friction, which reduces energy consumption during processing and increases resistance to built-up edge.
The SumoTec coating process reduces microcracking on the blade surface due to shrinkage when the blade is cooled after CVD coating. Similarly, the process eliminates harmful droplets on the surface of the coating during PVD coating, resulting in a smoother surface, resulting in lower cutting temperatures, longer life, and better chip flow during processing. And can use higher cutting speeds.
Another example is Isca's Do-Tec coating technology. This technique deposits a TiAlNPVD coating on a medium temperature CVDAl2O3 coating. This composite coating has excellent wear resistance and chipping resistance, and is very suitable for various blade grades for high-speed cutting of cast iron. Its expected cutting speed can reach above 650-1200sfm (depending on the type of workpiece material and Processing conditions).
Fifth, the preparation of the cutting edge
In many cases, the preparation of the cutting edge of the blade (or edge passivation) has become a watershed that determines the success or failure of the process. Passivation process parameters are subject to specific processing requirements. For example, the blade-to-edge passivation requirements for high-speed finishing of steel are different from those used for roughing. Cutting edge passivation can be applied to the machining of blades of almost any type of carbon steel or alloy steel, while the application of stainless steel and special alloy materials has certain limitations. The amount of passivation can be as small as 0.007 mm or as large as 0.05 mm. In order to enhance the role of the cutting edge in the harsh processing, it is also possible to form a minute T-shaped ribbed strip by passivation.
In general, blades for continuous turning and milling of most steel and cast iron require a greater degree of edge passivation. The amount of passivation depends on the grade of the carbide and the type of coating (CVD or PCD coating). For severely interrupted cutting inserts, heavy passivation of the cutting edge or the machining of T-ribbons has become a prerequisite. The amount of passivation can be close to 0.05 mm depending on the type of coating.
In contrast, since the blades for processing stainless steel and superalloys tend to form built-up edges, the cutting edges are required to remain sharp, only slightly passivated (as small as 0.01 mm), and even smaller passivation can be customized. Similarly, blades for machining aluminum alloys are also required to have sharp cutting edges.
For example, Isca produces a variety of inserts having a helical cutting edge that is contoured to move uniformly around a cylindrical surface in the axial direction. One of the advantages of this spiral-like helical blade design is that the cutting motion is smoother. Unlike the cutting method of the straight edge, the helical cutting edge simulates the movement of the spiral groove end mill. The cutting edge gradually enters the cutting during the "spiral" motion, rather than entering the cutting at the same time, thereby reducing chatter and achieving a better machined surface finish.
In addition, the helical cutting edge can withstand greater cutting loads, resulting in higher metal removal rates while reducing stress. Another advantage of the helical cutting edge is the extended tool life due to the reduced cutting pressure and cutting heat applied to the tool. Understanding the mechanism of tool wear and competing with new technologies can increase tool life and process efficiency. In today's market, companies not only have to compete locally, but also participate in global competition, so it is important to make full use of all of their competitive advantages.
Metal Hole Saw,Carbide Big Hole Saw Bit,Metal Hole Saw Bit,Hole Saw Cutter Bit
Danyang Yongshun Tools Co.,Ltd , https://www.china-drill-bit.com